/Workforce-Management-Solutions-Obliterating-Production-Bottlenecks.jpeg?width=900&name=Workforce-Management-Solutions-Obliterating-Production-Bottlenecks.jpeg)
At the most basic level, all businesses are very similar. All businesses take in some kind of raw material, whether it is iron ore, ingredients or information, processes it in some way, and outputs finished products. These business processes are always subject to restrictions that limit the maximum production capacity. When one of these restrictions severely limits production, it is often referred to as a bottleneck. One of the primary challenges of business process management is to find and eliminate bottlenecks in production.
Four Step Plan
The first step to eliminating bottlenecks is to always hire high-quality workers who have the skills you need. Skill gaps in your workforce require you to offer additional training, at a potentially significant cost. Furthermore, when your employees are stuck in training, they are not doing their jobs; this further handicaps production. Many businesses turn to workforce management solutions providers to help them find and hire the best workers. These providers specialize in finding and screening potential employees for their clients. Interviewing only prescreened applicants makes the selection process run much more smoothly. This is better for both the applicant and your business.
Read: Workforce Management Solutions—What Drives Excessive Overtime?
Employee skill gaps can lead to some bottlenecks, but others may be caused by inherent flaws in the organizational structure of a worksite or business. The only solution to these bottlenecks is to reorganize. A good strategy for reorganizing workers is to divide the business process into discrete steps or functions. These sub processes represent the necessary divisions of the organization. Assign a minimum number of workers to each of the tasks, and then assign more workers to the tasks that are slowing down production. To determine your management needs, start by evaluating how many managers are actually required. At a minimum, each division requires a mid-level manager, and similar divisions should be grouped together under the supervision of an upper-level executive. Workforce management solutions services can be helpful in these types of reorganizations. By doing a large-scale reorganization in this manner, neither the workers nor management feel as though they're being unfairly singled out for potential downsizing.
Invest in your employees by giving them the training and encouragement they need to reach their potential. Make sure each employee realizes what his or her role is, and how crucial this role is to the continued success of the business. Give all workers this type of big picture analysis. Stress how important it is to have every employee performing at his or her best ability to maximize productivity. Employees who see themselves as an important part of your organization will probably be more accepting of any training that is required.
Read: What A Contingent Worker Really Wants From Your Management Team
Finally, set realistic production goals for each day. Make sure every manager knows what is required in his or her division. If necessary, discuss staffing needs with your managers. Division managers should relay the daily requirements to the employees they supervise, so that everyone from top to bottom will know exactly what is expected of them. When you set goals for workers who have the skills to do the job and understand the value they bring to your business, these workers will tend to work hard to fulfill your positive expectations of them.
To evaluate your business processes and staffing needs, contact a workforce management solutions provider today.
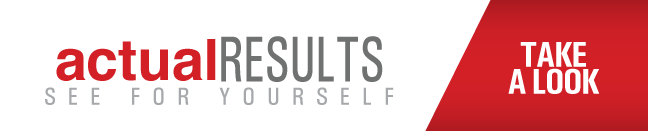